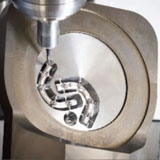
WORKNC Dental CADCAM cuts it for cosmetic dentistry experts Migros Dental
Continuous innovation
Migros Dental S.A., based in Madrid, has been specializing in manufacturing high quality dental prostheses since 1959. It pioneered the production of gold ceramic bridges in Spain. It now offers other techniques for fixed prostheses and prostheses on implants to produce the most aesthetically pleasing results. The company started producing zirconia cemented caps in 2003, and in 2006 upgraded its capability to offer bridges secured with threaded implants in the same material. Zirconia offers superior strength and toughness but requires CAD CAM techniques to machine the complex shapes involved.
Migros has 7 years of experience in CNC machining and was looking for an open system to complement its advanced 3D CAD and enable it to produce 5-axis CNC toolpaths on its DMG machine. Mario Tébar of Migros says, “We are continuously innovating the technology we offer and always developing new manufacturing methods so that we can supply our customers with the most advanced products. Our objective has always been ‘aesthetics with ceramics’.”
WORKNC Dental fits well with our policy of developing new aesthetically advanced prostheses. Not only has it reduced the production time for zirconia products and optimized the performance of our DMG machine, but it has also given us the ability to develop new techniques for the future.Mario Tébar, Migros Dental S.A.
Automatic, reliable 5-axis
The company was searching for an automated solution. Mario Tébar adds, “We chose WORKNC Dental CADCAMfor the way in which its machining wizards help us to rapidly generate reliable 5- axis CNC toolpaths. We can take CAD models from our 3D design system straight into WORKNC Dental. Its intuitive interfacemakes turning these into toolpaths very easy indeed.” For Migros, the speed and reliability of WORKNC Dental reduces production time significantly and makes it possible to cut the complete prosthesis in 5-axis in one setting. Collision avoidance considers the machine kinematics, automatically introducing flip and unwind movements, to facilitate manufacture. Within the wizards in the software, cutting strategies are optimized to suit each type of material. Migros cuts titanium, chrome cobalt and zirconia so, with WORKNC Dental, feeds, speeds tooling and methods are all automatically tailored to produce the best possible results for each, with virtually one mouse click.
Speed and accuracy
As well as speeding up and optimizing production, the ease of use of WORKNC Dental allows technicians unfamiliar with CNC machining to operate the system successfully. Unusually for dental laboratories, Migros has significant experience in this area, however the rapid production of 5-axis toolpaths is a complex process and its automation in WORKNC Dental allows technicians to spend more time using their core dental reconstruction skills. Mario Tébar says, “The software enables us to machine customized t i tanium abutments very accurately from a homogeneous block of material. The precision possible with WORKNC Dental facilitates ceramic lamination, producing a long lasting and robust prosthesis.”
Flexibility and scope
With the WORKNC Dental CAD CAM solution, technicians can work from scanned data, manipulate it in their chosen CAD package, and transfer it into CAM for machining on their individual machine tool. The open nature of WORKNC Dental allows users to select the most appropr iate equipment for their needs and accept data from multiple sources, in formats such as STL, giving them the opportunity to evolve new ideas and utilize the latest materials. Mario Tébar says, “We can accept design data from virtually any CAD system, which considerably enhances our flexibility. The technology within WORKNC Dental has also enabled us to increase the range of products we can offer, including prostheses and bars on implants, titanium hybrid structures, and zirconia abutments.”
Development of new advanced techniques
As well as chrome cobalt, titanium and zirconia, WORKNC Dental supports machining on the latest hypoallergenic materials such as PEEK, and has the ability to compensate for the shrinkage during the firing of sintered materials. 5-axis machining allows faster production and the ability to use shorter, smaller and more rigid cutters, while nesting and automatic location of support pins makes the best use of the material and ensures safe machining operations. Mario Tébar concludes, “WORKNC Dental fits well with our policy of developing new aesthetically advanced prostheses. Not only has it reduced the production time for zirconia products and optimized the performance of our DMGmachine, but it has also given us the ability to develop new techniques for the future.”